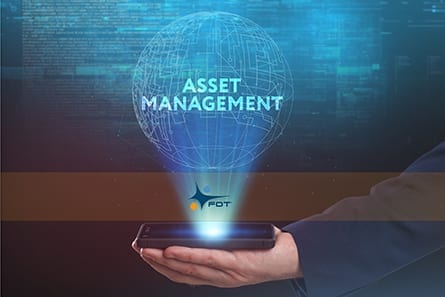
Author: Suriya Selvaraj, VP of Technology – FDT Group
For industrial organizations, asset management practices are critical to ensure the reliability and availability of critical equipment while keeping maintenance costs to a minimum, and to capitalize on short-term opportunities in the market.
FDT Group has long focused on bringing plants, people and data together. The organization’s latest development effort transitions its integration standard to an information exchange platform. This enables cloud-based asset monitoring for field devices, which reduces maintenance costs, improves asset reliability and provides useful information to personnel in a timely manner.
Today’s reliability challenges
In today’s industrial facilities, “smart” field devices are the eyes and ears of automation. They are able to provide more and more information and transmit it via bus systems to other components in the control network. However, the failure of a device can quickly lead to a malfunction of production equipment.
Traditionally, asset performance monitoring approaches involved monitoring devices for evidence of incorrect operation, pending failure or the need for calibration. This activity was undertaken with asset management programs or custom-written programs hosted on a desktop or client/server architecture based within a single facility. Users received reports for actionable items, and could utilize status displays showing where attention was required.
Emergence of the IIoT
The Industrial Internet of Things (IIoT), along with Industry 4.0, is one of the most significant trends in industrial automation. IIoT-based asset management solutions typically include condition monitoring, predictive maintenance, asset integrity management and reliability-centered maintenance, and often involve technologies such as asset health data collection, visualization, and analytics. They improve upon traditional asset management through deeper integration with enterprise resource planning (ERP) and computerized maintenance management systems (CMMS) – driving efficient and accurate maintenance work orders.
Accessible from a mobile device such as a smart phone or tablet, the latest IIoT-based solutions provide immediate awareness of performance/health issues by alerting engineering/maintenance personnel of an asset needing attention when they are near the installed equipment. The tools also make documentation and diagnostics immediately available. Technicians can view current versions of electronic manuals and device status while in the field.
Growth of cloud-based applications
The collection of data at a central point in the cloud has key benefits for the transparency and analysis of asset performance information. By establishing a single infrastructure to support multiple facilities, industrial organizations can leverage global expertise, spread costs between different stakeholders, and improve overall system availability. With this approach, it does not matter if data comes from multiple locations within one plant or several facilities that may even be distributed around the world; centralized data access allows users to run various statistics for a comparison/benchmarking of individual production lines or plants. An expert at one location can provide more value by being able to consult with other facilities as well.
In addition, the use of mobile devices for viewing data allows industrial operators to react very quickly to unexpected events, changing environments, and continually optimize their bottom-line results. This development also fits closely with modern workers’ expectation of connectivity to their data with easy access to it; and having a collaborative environment, so they can share information with their colleagues on the plant or factory floor.
Using FITS to optimize assets
The specialized equipment required for industrial manufacturing has become a focal point for concerns about operational efficiency, preventive maintenance, and costly failures that can harm business relationships and finances. This explains why cloud-based asset management solutions are becoming an essential tool for operating companies of all sizes.
FDT Group, an independent, international, not-for-profit industry association supporting the evolution of FDT® technology, has demonstrated that open industry standards bring value. FDT is the industry’s most widely deployed asset management solution, with tens of millions of FDT/DTM-enabled devices in use and hundreds of thousands FDT/FRAME-enabled host/systems installed worldwide. All major control system and device vendors support the technology.
Experience has shown that FDT/DTMs are a universal tool for lifecycle management of any device/network in the process and discrete automation markets. Indeed, they are intended for smart devices providing data-driven business intelligence. Their data allows for predictive maintenance models for effective asset support strategies.

The emerging FDT IIoT Server™ (FITS™) standard, set for release as part of the FDT 3.0 offering by year-end, will further empower the intelligent industrial enterprise with native integration of the OPC Unified Architecture (OPC UA), as well as Control and Web Services interfaces for mobile applications. FITS also encompasses a robust security solution to safeguard critical automation information and operating data. The standard provides enhanced protection measured via robust multi-layered security, and leverages vetted industry standards such as Transport Layer Security (TLS), Web Sockets Secure (WSS) and Hyper Text Transfer Protocol Secure (HTTPS).
FITS can be utilized in a host of diverse operating environments due to its platform independence within the .NET Core framework. This results in an FDT Server that is deployable on a Microsoft-, Linux- or iOS-based operating system. The solution enables cloud, on-premise, edge and desktop deployment methods meeting the needs of the process, hybrid and discrete sectors.
The FDT Server is built around a Core Server, which serves as a center point for wide range of client/server interactions. It includes an OPC UA Server providing access to DTM data with authenticated OPC UA Clients, and a Web Server enabling the use of web user interfaces on remotely connected, browser-based clients and other mobile device such as smart phones, tablets, and PCs. The solution also supports the use of apps that improve workforce productivity and plant availability.
Users can connect an FDT Server in the cloud to one or more plants with a secure virtual private network (VPN). This approach ensures full authentication and data encryption, and automatic tunneling through networks allows the system to directly talk with devices in the field. It also enables remote diagnostics by authorized users, so supervisors, managers and other stakeholders can monitor status on a remote basis.
FDT Group’s latest development allows for the creation of web-based DTMs™ that will seamlessly integrate with any FDT Server (multi-user) or desktop (single-user) hosting environment. These DTM-enabled devices serve as the source of data driving robust asset management capabilities. At the same time, integration with OPC UA provides an ongoing infrastructure to make this information available to thousands of other applications and platforms.
A key feature of the FITS platform is a cloud-based DTM repository, which enables all certified DTMs (based on FDT 3.0) to be automatically downloaded from the cloud for use in on-/off-premise and desktop applications. The repository provides convenient DTM/App storage and device management, as well as secure data transfer and messaging with proactive user alerts when DTM updates are available. The repository eliminates the headache of distributing DTMs, and instead provides a secure portal allowing vendors to authorize/de-authorize customers; view reports and download history; and upload, update, remove, or suspend DTMs as needed.
Advantages for industrial operations
With the FITS solution, industrial asset management becomes much more empowered thanks to better diagnostics and easier access to device information, reducing downtime improving meantime to repair (MTTR) performance. Users will be able to take advantage of secure and seamless data exchange/interrogation from sensor to cloud, and achieve new levels of information technology (IT) and operational technology (OT) integration. For device vendors, next generation DTMs will provide fit-for-purpose solutions for tasks such as deep inspection diagnostics and prognostics enhanced driven by artificial intelligence.
All DTMs based of FITS comply with the NAMUR NE-107 recommendation, which stipulates that operators need a view of the process including the status of the instrumentation in a simple and uniform way – regardless of source device – to support predictive maintenance strategies. The DTMs will be an important enabler for apps intended to view the health of field devices, and subsequently improve maintenance workflows.
As a platform-independent solution, FITS will benefit companies that operate plants with a diverse array (or brands) of automation systems and devices. It supports real-time monitoring and predictive maintenance applications requiring uniform access to field devices across platforms. The technology also supports enterprise control so that a single cloud instance can address multiple facilities to reduce costs, minimize overhead and centralize administrative tasks.
With FITS, field device data and information can be automatically provided for transport into cloud-based applications. This opens up the way for condition monitoring functions to be realized as cloud-based applications – independent of the automation system. The collected data can also be transferred using an export function for further processing in enterprise asset management or cloud-based condition monitoring systems.
The FITS solution will empower plants and factories with important benefits such as:
- Low total cost of ownership via truly open technology
- Robust device configuration, commissioning and diagnostic support
- Simplified engineering and increased productivity
- Reduced downtime (no more wasted maintenance)
- Predictive device maintenance approach to help identify problems before they become severe
Going forward, adoption of the versatile FITS platform will create opportunities for asset management as a service, with service providers completely managing the cloud environment and implementing a variable cost model based on the number of users and assets to be covered.
Conclusion
FDT Group’s technology, as advanced by its FITS solution, holds the key to monitoring critical plant and factory operations to reduce costs associated with facility maintenance and installed smart devices. It makes device data available when and where it’s needed for automation, asset management and engineering systems, delivering important performance information to support operational excellence.